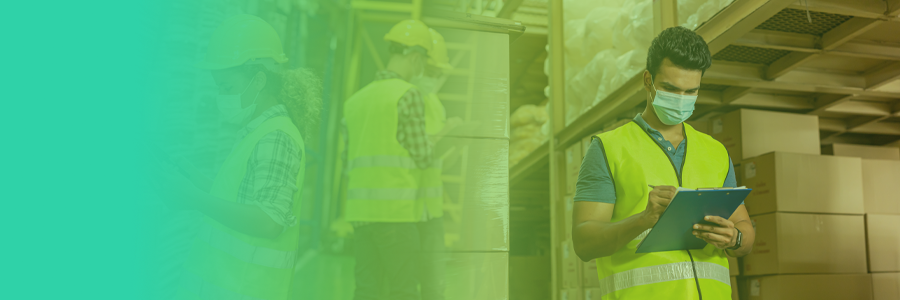
In just over a year, the transportation and logistics (T&L) industry has transformed, driven by a surge in digitisation and online shopping, unpredictable markets and fluctuating demand. Here are three ways your warehousing operations can continue to adapt in 2021 and beyond.
1. Streamlined Packages
Production companies are continuing to investigate growing customer trends and are looking to create customised packaged goods and offers to stay ahead in the market. Streamlining their packaging is an effective way to create more warehousing and operational efficiencies. Some of the immediate benefits are that staging of warehouses becomes faster. Picking and packing required for shipment at a fixed scope and price enables clarity of shipment dates – and with delivery dates aligned to customer’s digital expectations. In an increasingly competitive sector, this will be key to getting your products to customers at a competitive price and quickly. These processes are impacting, and even setting up, customer expectations as well as driving online demand. Our 2021 retail report, From Bricks to Clicks: State of Mobility in Retail 2021, highlights how 38% of customers would shop elsewhere when shipment and pick-up takes more than two days.
Focusing on improving operational efficiencies by being agile and creating new workflow solutions will be key. Not everything has to be standardised and formulaic. Let us look at BIC as an example. Their drivers needed to improve the accuracy, efficiency and timing of over 10,000 product packaging projects. Workflow alignment across their packaging and enhanced communications technology to better collaborate with customers, increased their time to market threefold. They enjoyed 100% automation of their packaging. Combined with improved collaboration, this prevented costly misprints and errors. New packaging has further benefited BIC with a threefold increase in delivery times on projects. By capitalising on custom project opportunities, BIC also increased the speed at which they deliver to their customers.
2. A Refocus of Technology in the Warehouse
The rise of e-commerce means delivery expectations have changed. The rise in transport costs, shortages of materials, breaks in the supply chain, alongside a rise in demand for drivers, has created a chaotic period of adjustment. An example of this massive adaptation is with online grocer Ocado who has invested £10 million with another British brand, Oxbotica, to build self-driving vehicles for itself and collaborators of Ocado to leverage. This enables automatic forklift trucks within warehouses to self-drive delivery vans or "kerb to kitchen" robots for the last mile
"Expecting the entire end-to-end operation to ultimately be autonomous, from the receipt of stock to the warehouse all the way through to the customer's door, has now become a reality. Organisations need to adapt and strive for growth in this competitive and fast-moving environment," says Stefan Spendrup, VP of Sales, Northern and Western Europe at SOTI.
According to our latest report, Mobilising the Delivery Workforce: State of Mobility in Transportation and Logistics 2021, 99% of respondents claim they are looking to implement technology to increase the speed of their operations’ performance, yet only 20% expect drones to be used to achieve this. It is time to consider introducing robots and enhancing automation – perhaps not across the board, but for some of the mundane tasks to help boost efficiencies in certain workflows and focus areas.
3. Integration of Full Production Plan Including Tighter Integration with Ethical Manufacturers
Carbon footprint assessments are mainstream and are essential from a compliance and supplier liaison viewpoint. Market awareness of located materials and their source is aligning to corporate responsibility and ethical business practices. Creating tighter integration and collaboration with manufacturers is also required to enable suppliers to source multiple alternatives to keep their chain moving should production or operations halt.
It also enables complete end-to-end process timeframes to be established and a more accurate expectation to be set with customers regarding delivery and supply. A full production plan incorporating the manufacturing and production of goods to the delivery into the warehouse, through to the order processing and consequent shipment out of the warehouse, is now a necessity. The visibility of this data at any time and location will be the key enabler.
Looking specifically at the automotive industry, the distinct lack of available resources in the past, such as Lithium and Cobalt, has caused production to halt of the Mercedes EQC and the Jaguar I-Pace SUV. Similarly, Audi and Jaguar Land Rover cited shortages in core components impacting battery production for their electric cars. The knock-on effects of this situation caused chaos down the supply chain as suppliers struggled to manage customer expectations and demands. This was all alongside commercial impacts and commitments to supplier and customer service level agreements (SLAs).
Lastly, knowing the fashion industry is one of the many impacted retail sectors during the pandemic, Bloomberg reports that 1,089 garment factories in Bangladesh have had orders in excess of $1.5 billion cancelled due to the coronavirus outbreak.
Better collaboration and visibility of the full supply chain, as well as an understanding of worker conditions and protection rights as part of an ethical supply chain, protects the most vulnerable and ensures that suppliers also commit to paying for cancelled orders. The ramification for a brand is huge up and down the entire supply chain, and data visibility is key along this entire journey.