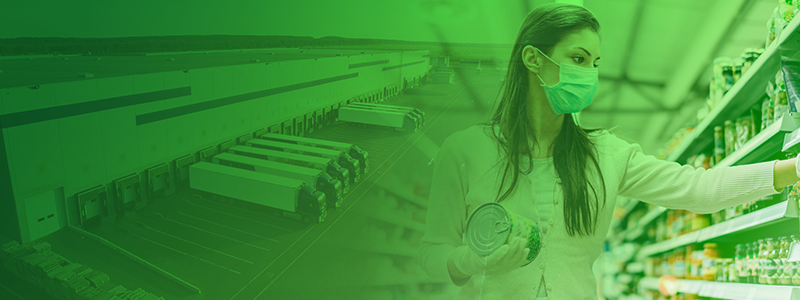
Beginning October 1, 2021, the UK Food Information Amendment 2019 (Natasha’s Law) will be rolled out in England, Scotland, Wales and Northern Ireland to all businesses selling Prepacked for Direct Sale foods (PPDS foods). This is food that is packaged at the same place it is offered to customers and is in the packaging before it is ordered or selected. Some examples include salads and sandwiches that customers select themselves, pre-wrapped foods kept behind a counter, or products that are packaged and sold at mobile or temporary outlets.
There are new labelling requirements on all food items that are prepacked for direct sale. Under Natasha’s Law the name of the food and a full ingredients list – with allergenic ingredients emphasised in bold, italics or a different color – must be clearly labelled.
While some of these updates may not seem new, they are causing complications and concern due to the depth of detail required, not to mention the assurances that suppliers, wholesalers and grocers will now require of all food ingredients from their suppliers. Navigating these changes will be critical to help business adapt to this ‘new normal’ in food packaging, labelling and selling.
Make Allergen Management a New Business Function
Allergen management needs to become a business function just as Food Safety Management is a core part of operational compliance. Implementing allergen management should be integrated within existing HACCP plans. Everyone has a responsibility to ensure the provision of correct allergen information. Continuous training to empower staff with the knowledge they need to keep operating needs to be a priority.
Suppliers must utilise an electronic food information management system to make managing information quick and easy between the organisation, staff and external suppliers.
Timeframes and notifications from wholesalers and suppliers to their customers about any changes to product information will become critical for enabling label updates on the shop floor. This industry change may enforce a tighter approved supplier list. Conversations with food sales reps will change from delivery dates and costs to agreed preferred brands and acceptable substitutions.
Heather Hancock, Food Standards Agency Chair, encourages all business to work with the Food Standards Agency to get this right: “Success will mean more choice and better protection for the millions of people – our families, friends, colleagues and neighbors across the UK – who have food allergies.”
What are the next steps for organisations like yours that will be impacted by these industry changes?
Organise Suppliers and Review Stock Inventory
Take the time to agree with wholesalers and suppliers the exact stock and brands required from now on, and do not accept alternatives as part of your inventory management system. This will help avoid any disruptions to labelling processes and mitigate compliance risks especially where automated purchasing systems are in place.
Now is the time to get your scanners updated to scan products in and track them through to sale when purchased. This data capture could all be required for compliance audits. Stefan Spendrup, VP of Sales, NWE at SOTI says, “A sophisticated mobile device control platform such as SOTI MobiControl can centrally manage mobile devices and ensure they are all up-to-date.” Documenting the various products to be shipped from the suppliers on route to the warehouse will help get the operational side ready for deliveries.
Barcode scanners provide proof of delivery and receipt of goods and their location; mini handheld computers with cameras provide photographs and proof of delivery for compliance requirements, all critical to enabling accurate labeling on shelves. Stefan continues, “An EMM solution within our integrated platform ensures devices are secured, operating effectively with the latest software, and that battery power is optimal. Data capture, reporting and analysis can be used to maximise efficiencies within any organisation. This will help the engine of any operation run smoothly while adjusting to these changes.”
It is unlikely to change every process and every device endpoint to make way for this new law. Regulations need to work within existing processes and operations. As such, bespoke applications and software updates are key to the rollout of this huge change for the food and drink industry.
Creating bespoke applications through a mobile app development solution to deliver the exact dates you need to meet supply chain and compliance requirements can really simplify the entire process. Different organisations have different software and hardware needs. Being able to develop and modify these changes – without the need for a costly developer – is an affordable, agile and cost-effective way to future-proof your operations.
Being able to easily manage the various brands with real-time click and ‘replace all’ functionality, simplifies this whole process quickly and easily.
Clearly Communicate Allergens to Staff and Supply Chain
There is no room for error here. Driving a communications plan and ensuring an audit trail of compliance is key. Organisations need to keep on top of this change and update their staff, suppliers and processes accordingly. Suppliers have a legal obligation to provide the exact ingredient composition of any food purchased from them.
Agility and flexibility in the food labelling process is key. Food allergen tools are available to help businesses decide what food and drinks need to be updated under the new law. Working with the SOTI ONE Platform can help ensure compliance, reduce downtime and enable robust connection to third-party labelling printers. This can help reduce the volume of tech required and reduce the impact to staff to simplify this shift as much as possible.
Use the Latest Software for Site Management and Product Updates
The challenges of supply chain management differ from site to site, so each must be trained in ensuring the correct provision of accurate allergen information.
Providing safe food with accurate information is a legal obligation. Getting stock in order is the biggest challenge and will take time to document the exact ingredient formulas to create each menu item. Once this is done, with the aid of food information management data, the process of labelling recipes becomes simple through a network of IoT-enabled devices that communicate with each other. This way organisations can reduce operating costs and increase the productivity of their workers and operations.
Once the system is updated, SOTI Connect can be used to link the mobile devices to a local printer where the information for the label is updated instantly.
Whether it’s a last minute change of brands with a different allergen profile or multiple recipes being batch loaded, an integrated mobile and IoT device management platform ensures all of this sensitive and business-critical data can be sent to all your mobile devices – each site and all impacted staff members – and be updated at the push of a button.
What Does the Future Look Like for Data Software and Labelling?
As products change and requirements from the Food Standards Agency are updated, it is likely that this will be a more ‘digital’ approach to providing up-to-date and exact details for consumers.
One thing is clear – this is a complex topic with many more specifics to review.